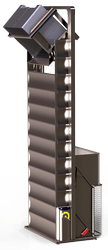
Vertical conveying of hygiene-critical bulk materials: a quick comparison
There are several options when it comes to vertical conveying of bulk material in a food-production line. Each has its merits. But some more than others.
To simplify things, we’ve distilled all the differences down onto one handy chart*:
![]() |
![]() |
![]() |
![]() |
|
---|---|---|---|---|
Characteristic* | Screw Conveyor | Spiral Belt Conveyor | Bucket Elevator | MegaDumper® SS |
High throughput capacity | ![]() |
![]() |
![]() |
![]() |
Small floor footprint, suitable for constricted spaces | ![]() |
![]() |
![]() |
![]() |
Gentle process, will not damage delicate grains | ![]() |
![]() |
![]() |
![]() |
Effectively handles any particle size | ![]() |
![]() |
![]() |
![]() |
Cost-effective at any height | ![]() |
![]() |
![]() |
![]() |
Fast and easy to clean - no inaccessible surfaces for bacterial growth | ![]() |
![]() |
![]() |
![]() |
Capable of handling liquids | ![]() |
![]() |
![]() |
![]() |
Low energy consumption | ![]() |
![]() |
![]() |
![]() |
Very low maintenance requirements | ![]() |
![]() |
![]() |
![]() |
*Characteristics have been simplified for the purposes of comparison.
As you can see, Simpro's MegaDumper SS comes out on top – especially when it comes to maintenance and hygiene. With a simple design and large, smooth surfaces the MegaDumper can be completely cleaned and sterilised in less than five minutes. What’s more, it can convey more than 20 tonnes of material an hour to heights beyond seven metres, while requiring a footprint of just two square metres.
The MegaDumper was introduced in 1998 and is used by dozens of leading food-processing companies, including Nestle, General Mills, Fonterra, Goodman Fielder, Cadbury, Tasti Products and Bundaberg Brewed Drinks. Learn more about the MegaDumper SS here, or ask Simpro for a free, no-obligation analysis and quote.