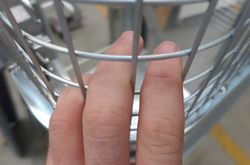
Machinery Guarding: the engineer's lowdown
Standards for machinery guarding have been in law since 1844, but you wouldn’t know it. Poorly-guarded machinery is still in use in workplaces everywhere – and each year claims a grisly toll of entanglement, crushing, amputation and dismemberment. Not to mention OSHA fines.
Crushed hands and arms, severed fingers, blindness - the list of possible machinery-related injuries is as long as it is horrifying. There seem to be as many hazards created by moving machine parts as there are types of machines. Safeguards are essential for protecting workers from needless and preventable injuries.
Basics of Machine Safeguarding - OSHA - United States Department of Labour
So it’s fair to say that machinery guarding is quite important. Here’s an engineer's lowdown on the subject, starting with we need it: hazards. There are six common hazards found on industrial equipment:
- Trap Hazards: parts of a moving system where body parts may be caught, resulting in crushing or entanglement. Look out for chains, belts, doors, feed devices and pivot points.
This is a big one in the world of lifting equipment – this crude bin-tipper, for instance, has a completely unguarded pivot mechanism:
- Impact Hazards: parts of a system which move rapidly and/or powerfully, and which might strike the operator or other personnel. High-speed machines often present impact hazards, including mixers, lathes and robotic arms.
- Burn Hazards: exposed hot surfaces. Examples include ovens, welders and heat-sealing equipment.
- Projectile Hazards: systems which could eject material at high speed in the event of failure. A common danger with lathes, drill presses and high-speed cutting tools.
- Friction Hazards: typically found in systems used to polish or abrade surfaces, such as linishers and sanding machines.
- Cutting Hazards: parts of a system where a sharp edge is used to sever materials. Common examples are guillotines and bench saws.
These six hazards should always be mitigated with effective, standards-compliant safeguards. There are eight types of safeguard in common use:
- Fixed Guards: these are panels positioned so as physically isolate the operator from the hazard. Fixed guards should be robust and difficult to remove; they are usually made from sheet metal, plastic or wire mesh.
Notice that poorly-designed fixed guards can be hazardous themselves – see how the mesh panels on this hydraulic lifter could crush the hand of an inattentive operator:
- Safety Interlocks: these are systems which disable the machine when fixed guards are removed or improperly positioned. The Simpro Dumpmaster and MegaDumper are both fitted with safety interlocks.
- Dual-Hand Controls: systems which require both hands to operate the machine, thereby preventing access to hazards while the machine is working. This approach only protects the operator, so should be used in conjunction with workplace safety training. Dual-hand controls are fitted on the Simpro Multi-Tip.
- Trip Guards: a photoelectric sensor which monitors the hazard area and disables the machine automatically when a body part or other object is detected.
- Adjustable Guards: these are fixed guards which can be moved into various positions to suit the task at hand. Adjustable guards may be easily disabled or removed, so should be used in conjunction with workplace safety training.
- Push-Away Guards: these are moving barriers which physically push the operator away from hazard areas while the machine is in operation. Since the barriers apply physical force to the operator, they must be carefully designed.
- Pressure Mats: floor matting fitted with weight sensors and installed in hazard areas. When the pressure of a person is detected on the mat, the machine is automatically disabled. Since this approach relies on complex electronic circuits, a parallel failure-monitoring system should be installed.
- Safe by Position: a safeguard approach based on ensuring hazard areas are inaccessible to personnel. This may involve plant layout or fencing, as well as workplace training.
Manufacturers with a professional approach to safety typically use a combination of these safeguards – and can provide compliance documentation on request.
There is no excuse for preventable injuries happening at work. Poorly guarded machinery and the lack of associated safety procedures remains a significant cause of death and injury in workplaces.
Ona De Rooy - Central Regional Manager - Worksafe New Zealand
The upshot is that machinery guarding matters. When considering new equipment, you should review the guarding for each type of hazard, and ask for safety documentation. If something looks like a shortcut, it probably is. Ask questions. And be prepared to pay a little more.
No-one regrets investing in the safety of their people.
